The Impact of Workplace Organization on Your Business
Posted: Tue Dec 10, 2024 9:43 am
A few years ago, I went on an early morning tour to Alcatraz Island in San Francisco Bay. The tour included a tour of Alcatraz Federal Prison. It ended in the kitchen, where a well-organized checklist made sure all the cooking utensils were in their proper places. Inmates were required to follow the 5S method to receive privileges beyond the bare necessities (food, shelter, clothing, and medical care). Over time, this helped to build a sense of pride in them, and the self-discipline they learned stayed with them when they had to reintegrate into society after their release.
More recently, I was able to watch an OB/GYN perform a delivery. All the medical instruments the team needed were right at their fingertips. (Needless to say, I was glad the medical team didn't have to leave the operating room to get instruments!)
I do my grocery shopping once a week. What a joy that the aisles are numbered and the items are labeled – instead of being piled up on the floor or hidden in a cupboard.
What do these three examples have in common? They all illustrate workplace organization or the 5S method.
What is workplace organization or 5S method?
Workplace organization, or the 5S method, was developed in Japan in the 1970s. It is a systemic approach to organization. It is not about "cleaning" or "spring cleaning." Rather, it is about setting up a system that, using visual cues, organizes the workplace in such a way that certain forms of waste are reduced and problems become visible earlier.
The 5S have been translated into French by the acronym ORDRE which means:
Organize – Sort out the things you use on a daily, monthly and yearly basis and keep on hand only those that are needed immediately. The rest should be labeled and stored elsewhere.
Tidying Up – Items should be stored in a functional manner, and visual aids, such as thumbnails, should be used to indicate to staff members where each item belongs.
Dusting – Ensure a clean work environment by removing dirt, trash and residue and establishing periodic cleaning schedules.
Make it clear – Teams should establish rules and work standards for common operational issues, such as what materials and tools to use and how information is communicated within the group.
Be rigorous or rigorous – An internal audit system should be established to ensure compliance with work methods. It should include regular inspections and a feedback mechanism on how to improve the process.
Read this article, 5S Method: Why a Cleaner Workplace Increases Productivity , to learn more about the 5S method.
Workplace organization is the starting point for many companies embarking on their journey to operational efficiency . It applies not only to the physical space (documents, machines, materials, etc.), but also to the digital space (information, data, files, documents). It is valid in a manufacturing organization as well as in a service company. And yes, I include service companies and digital spaces. (Think of the files and folders on your desktop or shared drive!)
Workplace Organization and Your Business
Most small businesses recognize the importance of a well-organized workplace and know how to go about achieving it, whether they've heard of the 5S's or not. However, they often implement only the first three "S's" (or the "Organize, Tidy, Dust Off" steps) and then conclude that the method doesn't work in the long run.
In November 2016, BDC held a national live webinar where participants were asked what their most pressing efficiency challenge was. Workplace organization was the most pressing challenge for 9.8% of business owners who participated.
This is unfortunate, since organizing your workplace using 5S is one of the most fundamental efficiency exercises you can do. The 5S method can have a positive effect on morale, reduce the risk of errors, and help staff members find tools and documents more quickly. This creates a more organized and safer work environment.
Workplace organization chart
Why should I organize the workplace?
Here are a few companies that I am sure you or someone you advertising database know has heard of: FedEx, Amazon, General Electric, Rolls-Royce, Toyota, and so on. I have visited some of these companies, and I have worked with and for some of them. These renowned companies have in common – as you may have guessed – the organization of their workplace or the 5S! I could easily extend this list by adding many SMEs.
Most large companies work with suppliers. The process of approving a new supplier company often requires a prior visit by members of the purchasing team. What do you think will strike members of the purchasing team when they visit your company? Yes – the lack of organization in your work environment.
In a previous job, I asked my purchasing team to start looking closely at the general cleanliness of a supplier’s premises before deciding whether to do business with them. We often found that a disorganized workplace was a sign of bigger problems. As your business grows, customers may want to check out how organized your workplace is or use it as a qualifying criterion before deciding that you are a supplier of choice! This is especially true in manufacturing.
There are many other benefits to implementing 5S in your business. For example, a BDC client in the Greater Toronto Area gained 10% more usable space and saw significant improvements in teamwork and employee engagement after implementing 5S.
Another client's management team that implemented 5S was surprised by how well staff members embraced the method and put it into practice. Another contractor confirmed that an organized and clean workplace makes a much better impression when customers visit.
The 5S method also addresses opportunity cost – when your staff is constantly searching for tools, data or information, they are not engaged in value-added activities. The impact of this constant searching can become significant over time. It’s apt to say that “small losses in operational efficiency will become big.”
Safety is another benefit of having a proper workplace organization system, so much so that some organizations now talk about the "6S" system, with the 6th "S" standing for safety.
What can you do to ensure that the 5S method is successfully implemented in your company?
Recognize that you and your leadership team have a role to play in sustaining the initiative over time.
Get trained on the method, and make sure your staff does too – education is the mother of improvement!
Start small – apply 5S to only a small part of your business (digital or physical space) first to get it right.
Give your staff the time they need to learn and apply 5S.
Celebrate successful implementations and associate them with rewards (tangible or otherwise).
What about your company? Are you struggling with clutter and disorganization in your workplace? Have you ever applied 5S? Join the conversation and let us know what you think.
More recently, I was able to watch an OB/GYN perform a delivery. All the medical instruments the team needed were right at their fingertips. (Needless to say, I was glad the medical team didn't have to leave the operating room to get instruments!)
I do my grocery shopping once a week. What a joy that the aisles are numbered and the items are labeled – instead of being piled up on the floor or hidden in a cupboard.
What do these three examples have in common? They all illustrate workplace organization or the 5S method.
What is workplace organization or 5S method?
Workplace organization, or the 5S method, was developed in Japan in the 1970s. It is a systemic approach to organization. It is not about "cleaning" or "spring cleaning." Rather, it is about setting up a system that, using visual cues, organizes the workplace in such a way that certain forms of waste are reduced and problems become visible earlier.
The 5S have been translated into French by the acronym ORDRE which means:
Organize – Sort out the things you use on a daily, monthly and yearly basis and keep on hand only those that are needed immediately. The rest should be labeled and stored elsewhere.
Tidying Up – Items should be stored in a functional manner, and visual aids, such as thumbnails, should be used to indicate to staff members where each item belongs.
Dusting – Ensure a clean work environment by removing dirt, trash and residue and establishing periodic cleaning schedules.
Make it clear – Teams should establish rules and work standards for common operational issues, such as what materials and tools to use and how information is communicated within the group.
Be rigorous or rigorous – An internal audit system should be established to ensure compliance with work methods. It should include regular inspections and a feedback mechanism on how to improve the process.
Read this article, 5S Method: Why a Cleaner Workplace Increases Productivity , to learn more about the 5S method.
Workplace organization is the starting point for many companies embarking on their journey to operational efficiency . It applies not only to the physical space (documents, machines, materials, etc.), but also to the digital space (information, data, files, documents). It is valid in a manufacturing organization as well as in a service company. And yes, I include service companies and digital spaces. (Think of the files and folders on your desktop or shared drive!)
Workplace Organization and Your Business
Most small businesses recognize the importance of a well-organized workplace and know how to go about achieving it, whether they've heard of the 5S's or not. However, they often implement only the first three "S's" (or the "Organize, Tidy, Dust Off" steps) and then conclude that the method doesn't work in the long run.
In November 2016, BDC held a national live webinar where participants were asked what their most pressing efficiency challenge was. Workplace organization was the most pressing challenge for 9.8% of business owners who participated.
This is unfortunate, since organizing your workplace using 5S is one of the most fundamental efficiency exercises you can do. The 5S method can have a positive effect on morale, reduce the risk of errors, and help staff members find tools and documents more quickly. This creates a more organized and safer work environment.
Workplace organization chart
Why should I organize the workplace?
Here are a few companies that I am sure you or someone you advertising database know has heard of: FedEx, Amazon, General Electric, Rolls-Royce, Toyota, and so on. I have visited some of these companies, and I have worked with and for some of them. These renowned companies have in common – as you may have guessed – the organization of their workplace or the 5S! I could easily extend this list by adding many SMEs.
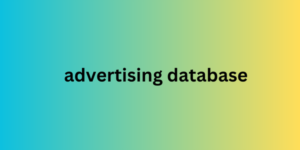
Most large companies work with suppliers. The process of approving a new supplier company often requires a prior visit by members of the purchasing team. What do you think will strike members of the purchasing team when they visit your company? Yes – the lack of organization in your work environment.
In a previous job, I asked my purchasing team to start looking closely at the general cleanliness of a supplier’s premises before deciding whether to do business with them. We often found that a disorganized workplace was a sign of bigger problems. As your business grows, customers may want to check out how organized your workplace is or use it as a qualifying criterion before deciding that you are a supplier of choice! This is especially true in manufacturing.
There are many other benefits to implementing 5S in your business. For example, a BDC client in the Greater Toronto Area gained 10% more usable space and saw significant improvements in teamwork and employee engagement after implementing 5S.
Another client's management team that implemented 5S was surprised by how well staff members embraced the method and put it into practice. Another contractor confirmed that an organized and clean workplace makes a much better impression when customers visit.
The 5S method also addresses opportunity cost – when your staff is constantly searching for tools, data or information, they are not engaged in value-added activities. The impact of this constant searching can become significant over time. It’s apt to say that “small losses in operational efficiency will become big.”
Safety is another benefit of having a proper workplace organization system, so much so that some organizations now talk about the "6S" system, with the 6th "S" standing for safety.
What can you do to ensure that the 5S method is successfully implemented in your company?
Recognize that you and your leadership team have a role to play in sustaining the initiative over time.
Get trained on the method, and make sure your staff does too – education is the mother of improvement!
Start small – apply 5S to only a small part of your business (digital or physical space) first to get it right.
Give your staff the time they need to learn and apply 5S.
Celebrate successful implementations and associate them with rewards (tangible or otherwise).
What about your company? Are you struggling with clutter and disorganization in your workplace? Have you ever applied 5S? Join the conversation and let us know what you think.